Challenge
The additional packaging volumes flowing through the Chattanooga DC were much higher than the customer expected, exceeding forecast by 35%. As a result, the existing VAS area layout and product flow design were suboptimal for the new volumes and the area was becoming overwhelmed. Kenco leveraged its corporate engineering team to conduct an emergency assessment and implement changes to improve throughput and meet the customer’s productivity goals.
Solution
The engineering team identified several “quick hit” improvements that could be made with minimal disruption to the packaging operation. They redesigned the packaging area into small, one- to two-person work cells. They removed unnecessary rollers that were now inhibiting product flow and representing a safety risk due to the increased number of associates working in the space. 5S was implemented across the new workstations to ensure everything was kept in the most optimal place for productivity and safety.
Results
The redesigned packaging area enabled an increase in units per labor hour from 22.18 to 28.15, representing a 27% improvement. This led to an annualized $184,000 savings in labor costs, as fewer associates were needed to accomplish the same throughput. The associates also enjoyed a safer, less
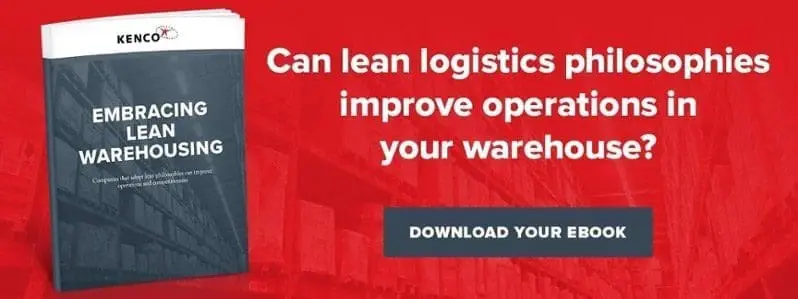