Challenge
A large consumer goods manufacturer challenged Kenco to improve site costs and increase throughput considerably to meet their network-wide budgetary goals. Several factors exacerbated this challenge. Both inbound and outbound volumes were consistently exceeding forecast while remaining highly variable, straining the operation from a labor planning standpoint. The need for a rapidly deployed labor management system (LMS) led to IT challenges that had to be addressed without impacting daily operations.
Solution
Kenco’s operations team approached the Kenco Innovation Labs to help support its improvement initiatives. The Innovation Labs was formed in 2015 and has quickly formed a reputation as an innovation leader in the 3PL industry with proprietary and iterative solutions. Our innovation team led a daylong Innovation Brainstorming Workshop with 20 site associates and leaders. After discussing pain points, the workshop employed several different ideation methodologies, including reverse brainstorming, to generated over 250 ideas for improvement.
Results
The improvement ideas touched on IT systems, process flow, layout design, training, and more. Once the ideas were generated, our Innovation Labs vetted and validated each concept, leveraging other resources as needed to quantify the savings impact and gauge the implementation requirements. In total, over $600,000 of cost savings were identified, and each idea was prioritized and incorporated into the site’s Hoshin Plan as part of the overall KOS Roadmap for Success. Within a few months of implementing some of the high-priority action items, the site has realized $80,000 of savings, $40,000 of which have hit the customer’s bottom line thanks to the gain/pain share program in place. With the transparent sharing of the workshop results and subsequent Hoshin Plan, the customer has greater visibility into overall health and progress of the site.
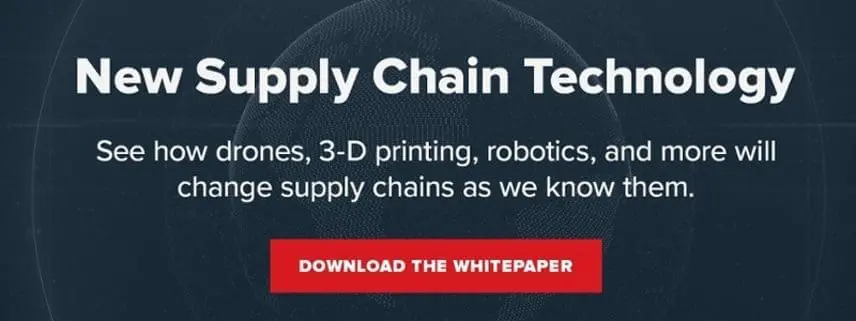